Монтаж печатных плат
Подготовка проекта под автоматический монтаж
Во многом качество SMT-монтажа обеспечивается еще на этапе проектирования печатного узла. Для того чтобы уменьшить вероятность возникновения проблем при монтаже, а также снизить его стоимость, необходимо учитывать требования предприятия, производящего монтаж. Их соблюдение позволит получить наиболее полную реализацию тех преимуществ, которые заключает в себе технология поверхностного монтажа.
Некоторые из приведенных здесь сведений носят общий характер и применимы к любому производству. Они основаны на рекомендациях и стандартах организаций IPC (Institute for Interconnecting and Packaging Electronic Circuits) и JEDEC (Joint Electronic Device Engineering Council). Другие сведения были получены нашими специалистами на основе собственного опыта работы с нашим оборудованием.
Применяемое оборудование позволяет размещать компоненты с минимальным расстоянием друг от друга 0,2 мм, а от края платы — 1 мм (при условии наличия технологических полей на заготовке). Но использование максимальных технических возможностей не всегда оправдано. Например, слишком близкое размещение компонентов очень сильно снижает ремонтопригодность изделия, оптическую инспекцию компонентов, проверку паяных соединений. Близкое расположение компонентов, разных по размерам и теплоемкости может сказываться на качестве пайки.
Кроме того, важно учитывать, что размеры корпусов многих компонентов выходят за размеры контактных площадок, поэтому при создании графики компонентов необходимо прорисовывать их реальные габариты или зону, занимаемую компонентом, с учетом пространства, необходимого для инспекции и ремонта. Это поможет правильному размещению компонентов и позволит избежать ошибок.
Рекомендуемые зазоры: 0,6...0,8 мм между чип-компонентами; 1 мм — между чип-компонентами и крупными элементами платы и 1,2...1,5 мм — между микросхемами и крупными компонентами, и 1,5 мм между SMD и выводными компонентами (см. рис.1).
Ориентация компонентов не имеет значения, т. к. на нашем предприятии метод пайки волной припоя не применяется.
Располагать SMD-компоненты на обеих сторонах печатной платы стоит только в том случае, если габариты платы, всевозможные ограничения на зазоры между проводниками, контактными площадками и другими элементами платы и прочие требования не оставляют выбора. В этом случае увеличивается затраты и время на подготовку и монтаж (изделие дважды проходит стадию монтажа, для него дважды пишутся программы на оборудование, дважды происходит его переналадка, изготавливается два трафарета, стоимость монтажа каждой стороны платы рассчитывается как за отдельное изделие). Кроме того, значительно возрастает стоимость тестового оборудования для проверки таких печатных плат.
Рис. 1. Расстояние между компонентами
В том случае, если одностороннее размещение компонентов невозможно, рекомендуется небольшие, например, пассивные, компоненты разместить на одной стороне платы, а микросхемы и другие «тяжелые» компоненты — на другой стороне.
На двусторонних платах тяжелые и крупногабаритные компоненты необходимо располагать с одной стороны печатной платы, чтобы избежать подклейки и/или проблем при пайке второй стороны.
Чтобы избежать перетекания припоя, произвольного смещения компонентов и других дефектов пайки, нельзя допускать расположения переходных отверстий на контактных площадках элементов или в непосредственной близости от них. Как уже говорилось, необходимо, чтобы контактные площадки компонентов были отделены от переходных отверстий, других контактных площадок и т.д. паяльной маской.
Подобное правило очень важно для микросхем с малым шагом выводов — их контактные площадки обязательно должны быть разделены маской. Переходные отверстия, расположенные в непосредственной близости от контактных площадок, необходимо закрыть паяльной маской.
Рис. 3. Контактные площадки и переходные отверстия
Элементы, расположенные внутри полигонов, должны быть отделены от них термобарьерами. Это позволит избежать неравномерного прогрева разных контактных площадок одного и того же компонента во время пайки и, как следствие, смещения этого компонента, дефектов «холодной пайки», «надгробного камня» и т. д.
Так же необходимо соединять контактные площадки и широкие проводники не напрямую, а узким проводником. Параметры этого соединительного проводника выбираются в зависимости от проходящего по нему тока. Это позволит избежать эффекта «холодной пайки».
Рис. 4. Разделение контактных площадок и полигонов
Одним из наиболее важных моментов при проектировании печатных узлов является соблюдение форм и размеров контактных площадок. Именно несоответствие этих параметров зачастую приводит к возникновению таких нежелательных явлений, как эффект «надгробного камня» или «транспаранта», непропай одного из выводов компонента, отсутствие контакта в паяном соединении, недопустимо большое смещение элемента. Поэтому при проектировании изделия необходимо учитывать рекомендации производителей компонентов, пользоваться их спецификациями, а для наиболее распространенных компонентов — стандартами IPC и JEDEC, и в частности, новым стандартом IPC-7351A, регламентирующим размеры контактных площадок и другие параметры печатных узлов, критичные для поверхностного монтажа плат.
Рис. 5. Маска между КП микросхем с малым шагом
При проектировании контактных площадок под компоненты в корпусе BGA мы настоятельно рекомендуем внимательно ознакомиться и следовать рекомендациям разработчиков микросхем. Среди общих моментов, касающихся контактных площадок таких компонентов, можно выделить следующее.
Контактные площадки BGA, также как и других компонентов, должны быть изолированы термобарьерами от полигонов питания и «земли».
Переходные отверстия должны быть отделены проводником и закрыты маской. Различают два типа контактных площадок под BGA в зависимости от вскрытия вокруг них паяльной маски: NSMD — Non Solder Mask Defined — не определенные вскрытием от паяльной маски, и SMD — Solder Mask Defined, то есть определенные паяльной маской. В первом случае площадка и небольшая область вокруг нее полностью вскрыты от маски (Рис.6а). Во втором случае вскрытие от маски выполняется с небольшим покрытием контактной площадки маской (Рис.6б).
Рис. 6. NSMD и SMD площадки BGA
Первый вариант обеспечивает большую прочность паяного соединения, за счет большей площади контакта и контакта с боковыми сторонами контактной площадки, а так же лучшее центрирование компонента и является более гибким и технологичным, как при производстве печатных плат так и при монтаже.
Преимуществом второго варианта является повышение прочности соединения контактной площадки и диэлектрика печатной платы. Его применение оправдано, если в процессе дальнейшей сборки, тестирования или эксплуатации плата может подвергаться значительным изгибам или другому физическому напряжению, а так же при эксплуатации при высоких перепадах температуры или если изделие будет проходить очень жесткие температурные испытания.
Если в документах производителя нет специальных указаний на тип площадки, рекомендуется применять NSMD тип.
Особенностью микросхем BGA является то, что их выводы скрыты под корпусом, что затрудняет проверку качества их монтажа. Основным средством инспекции паяных соединений таких микросхем является рентгеноскопический контроль. Но и в этом случае некоторые дефекты, даже такие как непропай отдельных выводов бывает сложно обнаружить. Для того, что бы повысить эффективность контроля пайки этих микросхем рекомендуется придавать контактным площадкам специальную форму (Рис.7).
При использовании таких контактных площадок паяное соединение принимает характерную форму, что значительно повышает эффективность проверки, особенно в автоматическом режиме.
Рис. 7. Площадки BGA, оптимизированные под рентген-контроль
На каждой плате необходимо предусмотреть наличие как минимум трех реперных меток, необходимых для систем технического зрения автоматического оборудования.
Реперные метки должны представлять собой круглые площадки диаметром 1 мм, вскрытые от маски на диаметре 3-4 мм. (Рис.8)
Они должны располагаться по углам платы (но несимметрично) и быть максимально удалены друг от друга (Рис.9).
Необходимо, чтобы проводники, контактные площадки, переходные, крепежные отверстия и другие элементы печатной платы располагались не ближе 5 мм от центра реперных меток.
Если на плате недостаточно места для размещения реперных меток, они должны быть размещены на технологических полях, что повлечет за собой увеличение их площади (Рис.10).
Рис. 8. Реперные метки
Рис. 9. Расположение реперных меток на плате
Рис. 10. Расположение реперных меток на заготовке
Если на плате размещаются большие металлизированные полигоны, то их необходимо размещать с обеих сторон платы насколько возможно равномерно, и выполнять в виде сетки из проводников. Это необходимо для предотвращения деформации платы при ее производстве и монтаже, при нагреве в печи оплавления.
Для оптимизации автоматического монтажа применяется панелизация - объединение нескольких небольших плат в мультизаготовку. Допустимые размеры печатного узла или мультиплицированной заготовки, состоящей из нескольких одинаковых плат, зависят от параметров оборудования, на котором будет производиться сборка. Для оборудования, которое применяется на нашем производстве, эти размеры должны находиться в пределах от 70х70 мм до 460х390 мм (допускаются отклонения в большую сторону, но это необходимо согласовать с нашими технологами). При этом рекомендуемое соотношение длины к ширине групповой заготовки примерно 3:2.
Наше оборудование позволяет осуществлять монтаж отдельных плат или групповых заготовок, не имеющих специальных технологических отверстий и полей. Однако в этом случае по длинным сторонам платы компоненты должны быть расположены не ближе 5 мм от края. Если поверхностно-монтируемые элементы размещены с обеих сторон платы, это правило должно соблюдаться и для второй стороны. В противном случае по длинным сторонам платы или мультизаготовки необходимо разместить технологические поля шириной 5 мм.
Рис. 11. Технологические поля
Для разделения плат между собой и технологическими полями существует два метода: скрайбирование (Рис.12) и фрезеровка по контуру платы. В первом случае по прямым линиям раздела плат и полей наносятся надрезы, которые оставляют в этих местах перемычку, размер которой определяет как жесткость всей заготовки в целом, так и легкость ее последующего разделения. Если платы будут монтироваться на автоматических линиях, используют более толстые перемычки, для обеспечения более высокой жесткости заготовки в целом. Для разделения плат в последующем используется специализированное оборудование, не создающее стрессовых нагрузок на печатную плату.
Для ручного монтажа и разделения эти перемычки делаются значительно тоньше, что обеспечивает легкое ручное разделение без последствий для печатной платы или спаянного изделия.
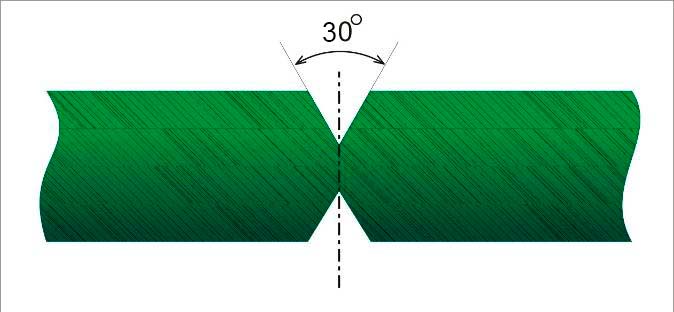
Рис. 12. Разделение плат скрайбированием
Если плата имеет сложный контур или требуется высококачественная и точная обработка этого контура, то разделение плат выполняется методом фрезеровки с формированием перемычек между платами и полями, которыми они объединяются в заготовку (Рис.13). По краям этих перемычек делается ряд отверстий, облегчающих их последующее разделение.
Для таких случаев необходимо на контуре платы предусмотреть места для размещения минимум 3-х — 4-х таких перемычек.
Подобный метод так же необходимо применять в случаях, когда на платы устанавливаются поверхностно монтируемые разъемы (USB, SIM, карт памяти и т.д.), габариты которых выходят за край платы. Иначе, при применении скрайбирования, корректное разделение заготовок на специализированном оборудовании будет невозможно.
Доступные варианты перемычек:
Также для снижения трудоемкости обработки сложного профиля рекомендуем комбинированный способ (вариант 1 + вариант 2).